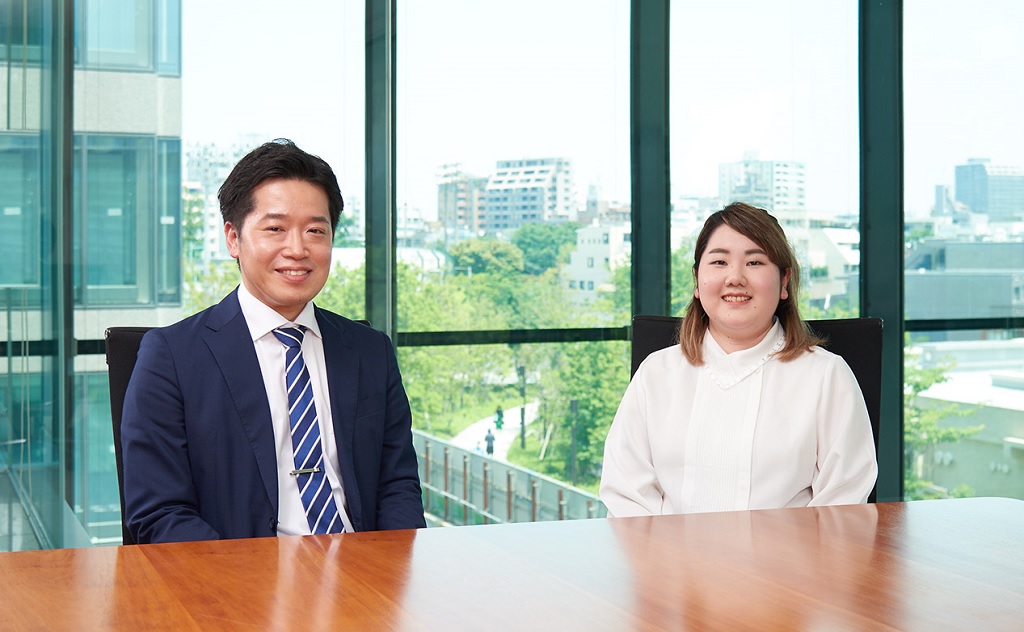
Devising an effective system to help reduce CO₂ emissions during the entire product life cycle
Many corporations in Japan and around the world are accelerating efforts to reduce greenhouse gas emissions and combat global warming. To support such efforts, Dai Nippon Printing Co., Ltd. (DNP) launched a certified system to calculate life cycle CO₂ (LC-CO₂) in April 2022. This is the first system authorized by Sustainable Management Promotion Organization (SuMPO) to automatically grant third-party approval to the calculated results of a product’s life cycle CO₂ emissions. The system, based on a technology that converts the emissions of greenhouse gases to those of CO₂, was developed thanks to the impressive teamwork of DNP employees and the company’s long-term commitment to reduce the environmental impacts of its products. The DNP Features Editorial Department interviewed Hitoshi Hamada and Miyuki Kamio, both of the Life Design Operations and key figures in this project, to learn more about the new system’s outstanding features.
- Visualizing the volume of CO₂ emissions directly connected to sustainability
- Combining team members’ different strengths and expertise creates new value
- Long-term experience in LCA and intracompany cooperation pivotal for success
- First certification under SuMPO’s scheme given to a system to realize time-saving, fair and reliable emissions calculations
Visualizing the volume of CO₂ emissions directly connected to sustainability
Reducing its environmental impact is vital for any corporation serious about ensuring a sustainable environment, society and economy along with their own sustainable growth. Disclosing information about the impact their corporate activities have on the environment has become increasingly important. This is particularly so against the backdrop of increased pressure to pursue so-called ESG management, which places a greater emphasis on environmental, social and governance factors. Furthermore, in recent years, corporations have increasingly been required to disclose not just their own emissions, but CO2 emissions from the entire supply chain of their products and services. Hitoshi Hamada was quick to sense this shift.
|
Hitoshi Hamada, Business Design Division, Innovative Packaging Center of the Life Design Operations
“I assumed my current section, which develops businesses friendly to the environment, in 2020. Since then, I have seen many clients request information regarding CO2 emissions in the life cycle of packaging materials made by DNP,” said Hamada. “Calculating life cycle CO2 emissions for packaging — from raw material procurement to manufacturing, transportation, disposal and recycling — has become the largest part of our work. So, it was natural that momentum to build a new calculation system would grow within our company.
“Accurately gauging LC-CO2 emissions is no longer simply desirable; it is increasingly required. We, therefore, focused on developing a certified system that would enable highly accurate LC-CO2 emissions calculations.”
Fig. 1 The range of CO2 emissions in the life cycle of various packaging to be calculated using the system (inside red frames) |
Hamada was one of the DNP employees involved in developing a system that calculates the LC-CO2 emissions of packaging. These calculations automatically receive third-party approval. By grasping their products’ LC-CO2 emissions, companies will be able to take specific measures to reduce these emissions. Disclosing this information to society also help corporations earn the support of institutional investors, other corporations, organizations and people at large for their environmental efforts.
“Previously, it was necessary to obtain third-party certification for the calculated LC-CO2 emissions of each product when we received calculation requests from companies and other entities,” Hamada said. DNP’s certified system to calculate life cycle CO2, on the other hand, received certification both for its management system and CO2 emissions calculation processes. This eliminates the need to obtain certification for each individual product, and the results can be swiftly provided as fair and reliable data with third-party approval. This will help efforts by companies and other entities to work toward carbon neutrality*1 in the entire product life cycle.”
Third-party certification of DNP’s system was granted by SuMPO. SuMPO’s vast experience in handling matters related to life cycle assessment (LCA) includes operation of the Japan Environmental Product Declaration Program. This program is known for quantitatively disclosing the environmental impacts in the product life cycle from the procurement of materials to their disposal and recycling.
- *1: Having a balance between emissions of carbon dioxide and other greenhouse gases from human activities and carbon sinks from tree-planting and forest management to achieve net zero emissions. Japan’s government declared in October 2020 that the nation will aim for carbon neutrality by 2050.
Combining team members’ different strengths and expertise creates new value
Miyuki Kamio played an important role as a bridge between employees involved in the calculation system’s management and those in the system’s development. Kamio handles information systems at the same department as Hamada. Her regular work involves managing personal computers and servers, but she was handpicked for this special role in her fifth year at DNP.
|
Miyuki Kamio, Technical Division, Product Center of the Life Design Operations
Kamio became interested in personal computers and acquired IT literacy after she encountered some spreadsheet software during a class at high school. “I participated in this project first by analyzing the old calculation tool that DNP had used to identify arguments*2 in calculation formulas,” Kamio said. “My job never involved the packaging manufacturing process, so I struggled to relate a CO2 emission calculation to this process.
“But I fully understood my team members’ earnest desire to develop the calculation system. I gradually learned about each member’s role. The management team wanted an easy-to-use system that reflects a product’s specifications, manufacturing, and disposal conditions. On the other hand, system developers at the information systems section wanted an automated system that can precisely calculate emissions under various conditions and, at the same time, leave some space to include more functions that might be required in the future.
“During my regular work, I deal with computers that each employee needs to carry out their duties. I naturally became a bridge between computer users and providers. Because of this, I was asked to serve as a facilitator between Mr. Hamada’s management team and the system developers during their regular online meetings. I set weekly goals for many people with various positions, expertise, and technologies, and then checked the progress made toward those goals. I focused on sharing information concerning their tasks and priorities so that everyone worked toward the same goal of building the system. I was delighted when I heard that my efforts were highly appreciated.
- *2: Values that are input in functions
|
Miyuki Kamio during the interview
Kamio now realizes that her environmental awareness increased through this project. “I gradually became more aware of this project’s social significance,” Kamio said. “Previously, I assumed that one individual’s actions, even sincere ones, could make little difference in solving environmental problems. But this project proved that I can actually get myself involved in efforts to reduce CO2 emissions.”
Long-term experience in LCA and intracompany cooperation pivotal for success
In 1993, DNP began prodding clients to consider — not only their appearance — but also how to reduce the overall environmental impact of their products when choosing their packaging. This necessitated looking at energy consumption during material procurement; packaging manufacturing and transportation; production of final products; and their disposal. In 1996, DNP introduced a life cycle assessment method to calculate its products’ CO2 emissions. DNP then compiled guidelines for eco-friendly product development from the viewpoint of reducing its products’ environmental footprint, based on how it designed and manufactured its products. In 2010, DNP developed the spreadsheet software-based calculation tool to calculate CO2 emissions, which later became the foundation for the latest system.
“The latest system is much more precise than the previous one and is designed to automatically give third-party approval to the results of the system’s calculations,” Hamada said. “Completing its development was challenging.”
|
Hitoshi Hamada during the interview
Hamada led the work to stipulate rules for calculating CO2 emissions and build a management framework for running the system. To ensure the system operates surely and smoothly, a new calculation tool (software) needed to be incorporated into DNP’s internal core computer system.
“When I told my colleagues at the information systems section about its importance, they understood fully and agreed to develop the new calculation system,” Hamada said. “During the development stage, we devoted considerable time to configuring how much waste is produced in the manufacturing process and deciding which information should be integrated into the calculation tool.
“We exhaustively discussed how to accurately reflect variable conditions — which were projected to arise from clients requesting various types of packaging — in the algorithm. For example, we prepared for situations in which we are unable to obtain necessary data from the order information of certain products, for which we will calculate LC-CO2 emissions. We also encountered many cases in which calculations become very complicated when all the elements were factored in. We often discussed, for instance, how each product’s emissions should be calculated, while repeatedly testing and applying the tool before completing its development. Despite knowing little about LCA when they started this project, the system developers learned quickly and accurately reflected our intentions in the system.
“The system management team included employees from the product and technology development departments to verify the calculation results. These internal validators had to take a SuMPO qualification examination, but the relevant departments and sections cooperated with us because this would help realize a decarbonized society. We are very grateful to them.”
First certification under SuMPO’s scheme*3 given to a system to realize time-saving, fair and reliable emissions calculations
DNP’s team sought SuMPO’s assistance from the system’s conceptual stage. But because this was the first certification under SuMPO's scheme and it was also the first by DNP to create a system that could approve its results, they initially were unsure about how to devise calculation rules that followed requirements set by the International Organization for Standardization (ISO).
The DNP team dealt with issues that SuMPO identified one by one. Take packaging for snacks, for example. Calculating CO2 emissions for such packaging must include the procurement of materials; making the packaging; transportation from a DNP factory to the client’s factory where the snacks are packaged; and disposal of used packaging. DNP examined in detail how much energy consumption and waste amount at each stage, and how it should be factored into the calculations. DNP also clarified a question from SuMPO as to how appropriate its automated calculation methods are once it became operational. Then DNP conducted Proof of Concept (PoC) and identified issues that required improvement. From early 2022, the team accelerated its work to finish the system, and in April, it successfully obtained the first certification under SuMPO’s scheme.
“I was cheering for the management and development teams from the bottom of my heart as I watched them working hard on the project’s final touches from early 2022,” recalled Kamio. “I felt a huge sense of achievement when I heard that we had obtained the certification.”
The system is capable of calculating LC-CO2 emissions for a wide range of packaging, including flexible packaging mainly made of plastics or paper, molded packaging such as rigid plastic containers, and paper containers. The system can even make calculations for other manufacturers’ packaging by conducting a simulation using DNP’s data.
DNP plans to widen the scope of packaging that the system can deal with. “We want to update the system so it makes calculations on all kinds of packaging and submit data on their CO2 emissions,” Hamada said. “By doing so, we’d like to create new value that would help attain carbon neutrality, which is essential for a sustainable society.”
DNP is now pushing ahead with a project to build another system, based on the latest one, to handle other products besides packaging.
-
*3: Carbon Footprint Comprehensive Calculation Scheme by the Sustainable Management Promotion Organization (SuMPO), a third-party organization.
SuMPO: Please refer to the following news release datelined October 1, 2021. (Japanese only).
https://sumpo.or.jp/news/release20211001.html
|
Expectations for DNP
![]() |
---|
Takehisa Kabeya, Managing Director of the Sustainable Management Promotion Organization (SuMPO) |
Visualizing the volume of LC-CO2 emissions and “communication among the entire supply chain” will be crucial in our efforts to attain a carbon neutral society. We have high expectations for the pioneering efforts undertaken by Dai Nippon Printing as a front-runner in the carbon neutrality initiative, and also as an entity leading effort in creating a society in which the benefits of a good carbon cycle are truly tangible.
What is LCA?
An evaluation method to quantitively assess how much energy and how many resources are used and how much impact is imposed on the environment during the life cycle of products and services, from the extraction of raw materials to manufacturing, transportation, usage, and disposal. The ISO has stipulated procedures to make LCA with the aim of prodding corporations and other entities to adopt manufacturing and other processes that reduce their environmental footprint.
Instead of comparing a certain life cycle stage of a product, such as the manufacturing stage, and determining whether one product has less environmental impact than the other, it is becoming more important to consider the whole life cycle of the product. LCA, therefore, is capable of clarifying the environmental impacts of products during their life cycle and providing data for developing eco-friendly products.
Fig. 2 Product life cycle |
- *Source for “What is LCA?” and Fig. 2: Seminar materials provided by SuMPO
Profile
![]() |
---|
-
Hitoshi Hamada
Business Design Division, Innovative Packaging Center of the Life Design Operations
Joined DNP in April 2006. After working on the development of a manufacturing process for paper containers at the Packaging Operations (now the Life Design Operations), Hamada was transferred in 2020 to the Innovative Packaging Center, where he heads the development of eco-friendly businesses. He participates in industry-academia collaboration projects.
![]() |
---|
-
Miyuki Kamio
Technical Division, Product Center of the Life Design Operations
Joined DNP in April 2018. She is in charge of managing digital devices and servers. During development of the latest system, she served as a facilitator between the management and development teams.
- *DNP department names, product specifications and other details are correct only at the time of writing. They are subject to change without prior notice.
October 13, 2022 by DNP Features Editorial Department
Discover more
Related products and services
DNP's Mono-material Packaging(Open in a new window)
This environmentally friendly package is made from a single material (Mono-material), maki...
DNP's Transparent Barrier Film (Open in a new window)
DNP's Transparent Barrier Film is a functional film that has superior moisture barrier and...