Product Safety and Quality
DNP recognizes that placing safety and quality first and foremost is a responsibility of a company providing products and services to society. Under this recognition, we strive to constantly improve by always exploring how our products and services are used and asking ourselves questions such as, “What are the quality requirements” and “What makes the products and services safe and easy to use” from the perspective of customers and consumers. Moreover, the initiatives we take for the safety and quality of products and services are based on our efforts to always consider people’s satisfaction throughout the supply chain from the proposal stage through to final delivery and from the procurement of raw materials to the manufacturing, use, disposal and recycling of products to increase society’s trust in us.
Medium-to long-term vision
We seek to gain the trust of society by prioritizing the safety and quality of our products and services as part of our responsibility as a company that supplies these to society.
SDGs Covered by the Vision
Performance Indicators to Monitor the Progress in Achieving the Vision and Activity Results
Performance indicators | Targets | Results |
---|---|---|
|
|
For most-recent fiscal year results |
- *1Including cases where a defect in our products jeopardizes the user’s life, causes serious bodily harm or inflicts serious damage on the user’s property (other than the product itself)
- *2Quality system inspection: Conducted by the head office’s quality assurance supervisory division, target sites are inspected once a year to check the operation of the quality management system
Structure to Promote Management
Internal Structure and Management
DNP’s basic policy concerning quality management is to ensure that our products and services conform to the required standards and legal regulations and to fulfill our corporate social responsibility by providing products and services that deliver levels of safety and quality exceeding the needs and expectations of corporate customers and consumers. To promote quality management, a Group-wide supervisory organization called the DNP Group Quality Assurance and Product Safety Committee has been established. It is chaired by the corporate officer in charge of the head office. We have stipulated Group-wide rules consisting of actions that should be taken to ensure the safety and quality of our products and services. We have also established a quality management system and a product safety management structure. Meanwhile, a Quality Assurance and Product Safety Committee has been set up within each of the business units and Group companies, the agents of our operations.
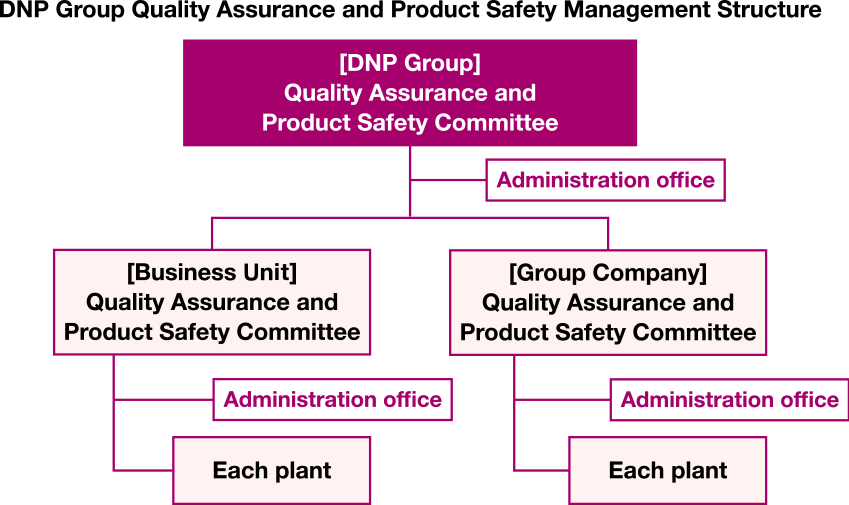
According to the Group-wide rules, the head office’s quality assurance supervisory division reports on the status of Group-wide activities, issues and other relevant matters twice a year to the DNP Group Quality Assurance and Product Safety Committee to review policies and targets and improve activities. To ensure greater safety and quality, the head office’s quality assurance supervisory division gives guidance to the business units and Group companies based on the results of discussions at the Committee’s meetings and engages in activities to prevent serious quality accidents and ensure that proper actions are taken in the event of an accident.
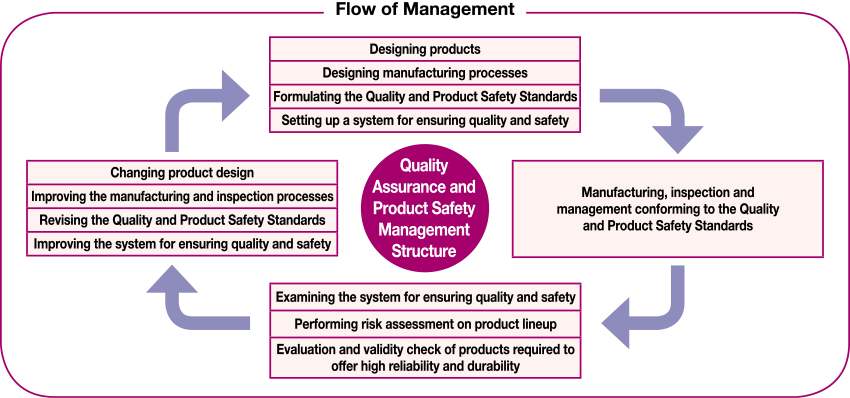
DNP anticipates demand from corporate customers and the marketplace and it has obtained many certifications relating to quality assurance such as ISO9001, an international standard for quality management, Food Safety System Certification (FSSC) 22000 in the field of food packaging and IATF 16949, a quality management system for the auto industry.
Acquisition of certification (Japanese site opens)(Open in a new window)
DNP’s Main Initiatives
Initiatives for Ensuring Product Safety and Quality
DNP identifies and evaluates risks impacting all of the products and services it provides from the design stage, and works to reduce the detected risks. DNP continues to offer products and services that make corporate customers, consumers and other people feel secure in terms of both safety and quality.
After the products and services are made available, we continue to monitor them through biannual risk evaluations and safety monitoring, thereby keeping up with the social and technological change of the environment. If the results of a risk evaluation call for a design change, an improvement of the manufacturing technology or other action to ensure product safety and quality, it will be implemented correctly and our internal standards will also be reviewed.
The head office’s quality assurance supervisory division conducts annual quality system inspections to check the operation of the quality management system and prevent fraudulent quality. The inspection is annually reviewed to ensure it stays effective. Inspection results are reported to the DNP Group Quality Assurance and Product Safety Committee and the Corporate Ethics Committee and, based on instructions from these committees, corrective actions are taken.
Employee Education
Based on its education plan, DNP provides the education necessary for all employees of the DNP Group to sincerely and rigidly work to ensure the safety and quality of our products and services. Employees may receive training in accordance with their job experience and job level. Our employee training program started in 1994 and, since fiscal 2000, all employees of the DNP Group have participated in it in the form of an e-learning program.
High-level specialized education is provided to people in jobs that require more specialized knowledge.
Thorough Verification in the Actual Use Environment and Control of Changes
DNP conducts tests, evaluations and verification in the actual use environment and more demanding conditions at all stages of the process from design to the release of the product, in accordance with the extent of the risks. In doing so, DNP seeks to ensure that users can feel safe and secure in using products and services before any decision to release them.
There is a similar process for decisions on the changing of the materials or shapes of a product, manufacturing methods and contents of services, etc. in association with the changing needs of corporate customers and consumers and the changing internal and external environments.
Internal/External Audit
- Internal audit: We conduct internal audits periodically in accordance with DNP’s unique initiatives and the ISO 9001 standard, irrespective of whether the ISO 9001 certification has been acquired.
- External audit: We are audited by corporate customers, outside certification institutions and equivalent organizations as appropriate. The results of the audits are reported to executives at meetings of the Quality Assurance and Product Safety Committees of the business units and DNP Group companies and are also shared with the head office’s quality assurance supervisory division to ensure proper feedback is provided.
Initiative for prevention of fraudulent quality
DNP strives to enforce legal compliance and ensure safety and quality. The Company sufficiently manages risks of legal violations and fraudulent quality and works to prevent them.
Amid the series of fraudulent quality incidents in Japan and overseas, DNP has been working to prevent similar incidents from occurring within. While we receive ISO and other external certifications and diagnoses, the head office’s quality assurance supervisory division checks the validity of our quality management system to reinforce the mechanism and provides the business units with guidance and instructions for corrective action.
Additionally, DNP are continuing departmental education on our Group-wide rules tailored to the employee’s role, including agreements with corporate customers regarding specifications, ensuring the reliability of inspections and other matters. DNP also continues to conduct case studies and awareness-raising activities to develop a corporate climate that looks to prevent fraudulent quality.
Quality Control in the Supply Chain
To ensure stable maintenance and the improvement of the quality of products and services, DNP cooperates with suppliers to continually and regularly evaluate and monitor products and services based on the quality management system and similar initiatives, and to seek solutions to problems and failures when they are detected. Quality is also controlled within the companies of the DNP Group, throughout the supply chain, based on Group-wide rules as we provide products and services to corporate customers and consumers to ensure they always feel safe about using the DNP Group’s products and services.